In today’s industrial landscape, the art of shaping metal into robust structures stands as a testament to human ingenuity. At the heart of this craftsmanship lies the intricate process of metal fabrication for steel sheet piling. This sophisticated technique, encompassing cutting, bending, and welding, transforms flat metal sheets into resilient structures vital in the construction and manufacturing sectors. From precision cutting to intricate assembly methods, each step in this process contributes to the creation of durable and functional structures.
The Essentials Of Metal Fabrication For Steel Sheet Piling
Metal fabrication for steel sheet piling is a sophisticated process that transforms flat metal sheets into diverse forms and structures. This procedure, applicable to various metals, including brass, steel, copper, and aluminum, involves cutting, bending, punching, and welding techniques. Notably, precious metals like gold and silver find their use in ornamental projects. The thickness of these metal sheets, also known as the gauge, varies inversely with the actual thickness, ranging from the delicate foil to the more robust plate.
At its core, metal fabrication for steel sheet piling revolves around converting sheet metal into practical components. This encompasses creating holes, shaping 2D geometric patterns, and even stretching to achieve complex contours or angles. The initial step involves cutting a precisely sized ‘blank’ from larger metal sheets, often sourced in flat, rectangular forms or rolls for thinner materials.
This technique plays a pivotal role across numerous sectors, including construction, automotive, aircraft, consumer goods, furniture, and HVAC, showcasing its vast applicability and importance in industrial and commercial projects.
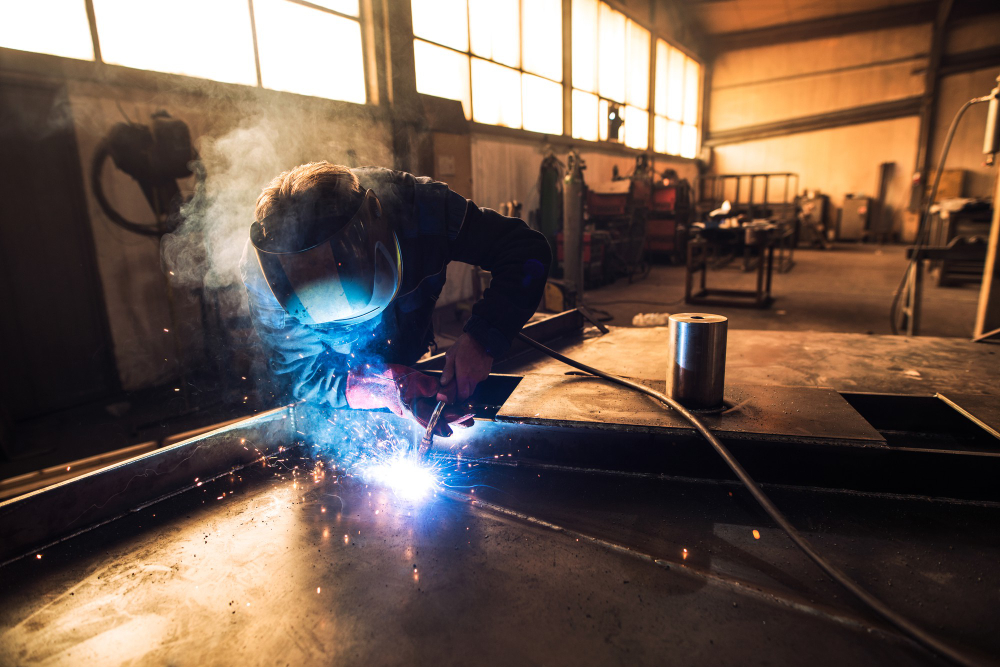
Metal Fabrication Techniques
- Cutting in Metal Fabrication
Metal fabrication for steel sheet piling involves precision cutting, a critical step that shapes the metal. This process utilizes a mix of tools ranging from handheld devices and power tools to advanced Computer Numerical Control (CNC) technologies like plasma torches and lasers. Cutting is essentially a subtractive method, where creating functional parts involves removing metal sections. It’s categorized into two: non-shear (using technology like lasers for clean cuts) and shear (using traditional methods like shearing machines). This diversity in techniques allows for intricate designs and shapes in metal fabrication projects.
Precision and Diversity in Metal Fabrication for Steel Sheet Piling
- Shear Cutting in Metal Fabrication
Shear cutting, an essential technique in metal fabrication for steel sheet piling, involves three main processes: basic cutting, shearing, and blanking. Basic cutting divides the metal into smaller pieces with a blade, serving as a foundational or standalone process. Shearing, akin to scissor action, employs stationary and moving blades to make straight cuts, praised for its clean edges and efficiency across various metal gauges without producing waste. Blanking, the most forceful, uses a punch to create holes, offering precision by removing material to be reused or discarded.
- Non-Shear Precision Cutting
For higher precision in metal fabrication for steel sheet piling, non-shear methods like laser beam cutting, waterjet cutting, plasma cutting, and machining offer advanced alternatives. Laser cutting, focusing intense light on slicing or engraving, excels in precision and energy efficiency but is optimal for thinner gauges. Waterjet cutting, combining high-pressure water with an abrasive, is ideal for softer metals, preventing heat-induced deformations. Plasma cutting is well-suited for various applications, cutting through metal with a plasma torch. Machining, including spinning and milling, removes material with specific tools, offering versatility in shaping metal sheets. Punch presses, utilizing shearing force, punch out diverse shapes and sizes, highlighting the adaptability of metal fabrication techniques for intricate and robust steel sheet piling projects.
Techniques In Sheet Metal Forming
Sheet metal forming stands out as a core part of metal fabrication for steel sheet piling, focusing on altering metal sheets into specific shapes without removing material. This involves various methods, each designed to meet different requirements.
- Bending Techniques
Bending transforms sheet metal into U-shapes, V-shapes, and channels using devices like press brakes, achieving angles up to 120 degrees. The process varies in complexity with the gauge of the sheet metal, where thicker gauges present more challenges. Decambering is a special form of bending that straightens strip-shaped metal pieces.
- Stamping Process
In stamping, a mechanical or hydraulic press, along with a set tool and die, alters the sheet metal without necessarily detaching any material. This technique is versatile, supporting operations like drawing, curling, and embossing, thus adding intricate details to the metal surface.
- Stretching Methods
Stretching reshapes the metal by elongating it over a die, facilitated by machines such as stretchers or English wheels. This process allows for the creation of large, contoured shapes on the sheet metal. The force applied, either hydraulic or pneumatic, stretches the metal while it’s secured by gripping jaws.
- Spinning Operation
Metal spinning leverages a lathe to mold the sheet metal into symmetrical parts such as cylinders or cones. This method, akin to CNC turning, involves pressing the metal against a rotating mandrel to achieve the desired form, showcasing the versatility of metal fabrication for steel sheet piling.
Integral Steps In Sheet Metal Assembly
Sheet metal assembly is a crucial phase in the fabrication process, binding various components into a cohesive unit. This stage employs numerous techniques and fasteners, such as bolts, rivets, and screws, to securely join parts. Techniques such as punching create the necessary openings for these fasteners, demonstrating assembly’s essential role in metal fabrication for steel sheet piling.
Welding Techniques
Welding stands out as a key method in assembly, leveraging heat to merge metal parts with or without additional filler material. This process results in a strong, fused joint that often surpasses the strength of the original materials. Various welding methods, including arc, MIG, and TIG welding, cater to different metal types and applications. The technique finds its use not only in metal joining but also in plastic and wood applications, showcasing its versatility.
Welding produces several joint types, including:
- Butt joints, connecting parts edge-to-edge.
- T-joints, joining the edge of one part to another’s face at up to a 90° angle.
- Corner joints, forming angles between 30° and 135°.
- Edge joints, with angles of 0° to 30° inclusive.
- Cruciform joints, where two parts are welded at right angles on a flat plate.
- Lap joints, linking overlapping parts at angles up to 5°.
Riveting – A Time-tested Joining Method
Riveting utilizes small metal pins to fasten sheet metals together. This method is efficient for creating strong joints without the need for heat, making it suitable for a wide range of applications.
Key rivet types include:
- Drive Rivet: Features a short mandrel, installed with a hammer to create a flared end.
- Blind Rivet: Ideal for inaccessible joints, this rivet is quick and versatile for sectors like electronics and aerospace.
- Friction-lock Rivet: Commonly used in aerospace for its secure fastening capability.
- Solid Rivet: A straightforward design, it fastens with its head directly into the material.
Metal fabrication for steel sheet piling relies on these assembly methods to construct durable and functional structures. Each technique, from welding to riveting, contributes to the overall integrity and utility of the final product, underscoring the importance of assembly in the metal fabrication process.
Key Equipment In Metal Fabrication
In the world of metal fabrication for steel sheet piling, specific equipment is indispensable for executing various projects effectively. These tools and materials not only enhance the quality of the finished product but also add efficiency to the fabrication process.
- Fittings: Essential for crafting and finalizing pieces, ensuring they meet project specifications.
- Plate Metal: Offers flexibility in shaping workpieces, serving as the backbone for various designs.
- Castings: Elevate the aesthetic appeal of fabrications, facilitating quicker production processes.
- Formed and Expanded Metal: Ideal for creating outdoor furniture, its design allows for moisture drainage, combining functionality with durability.
- Flat Metal: Enhances fabricated items with visual appeal and texture, crucial for crafting diverse shapes.
- Sectional Metals: Includes L-beams and Z-shapes alongside rod and bar metal, pivotal for segmenting and structural support.
- Welding Wire: Available in multiple thicknesses, this tool is vital for the welding process, aiding in the seamless joining of metal pieces.
These components collectively contribute to the versatility and efficiency of metal fabrication for steel sheet piling, ensuring that projects not only meet the desired standards but also withstand the test of time.
Unlocking The Power of Steel Sheet Piling
Ready to elevate your steel sheet piling projects to new heights? Partner with Bigfoot Pipe & Piling for top-notch expertise and quality materials. Our team is dedicated to delivering exceptional results, whether you’re tackling construction, infrastructure, or marine projects. Contact us today to harness the power of steel and take your projects to the next level.
Get Started Today
Looking for the right materials for your project? Contact us today and let our team provide you with the best solutions to fit your needs.